American automakers once commanded unwavering consumer loyalty, their vehicles representing the pinnacle of reliability and engineering prowess from the 1930s through the 1960s. Then came the perfect storm of energy crises, foreign competition, and corporate arrogance that transformed trust into betrayal.
Quality plummeted faster than a Citation’s resale value as Detroit prioritized profit margins over engineering integrity. Bad decisions compounded into catastrophic failures that rewrote the entire automotive landscape.
5. Chrysler R-Body Cars (1979-1981) (Exterior)

Chrysler’s R-bodies looked like automotive fossils because they essentially were—rolling relics built on platform technology that belonged in the Smithsonian, not competing against efficient Japanese engineering marvels. The Newport and New Yorker stretched longer than a city bus while displaying all the aerodynamic sophistication of a brick warehouse—a design lineage that can be traced back to some of the most hideous cars from the 1960s.
These behemoths featured massive chrome grilles and bumpers that screamed “old America” while Honda and Toyota offered sleek, purposeful designs that actually acknowledged the existence of fuel efficiency. Seeing an R-body navigate modern traffic was like spotting a mastodon trying to race greyhounds—impressive in its own prehistoric way, but utterly wrong for the times.
Chrysler R-Body Cars (1979-1981) (Interior)
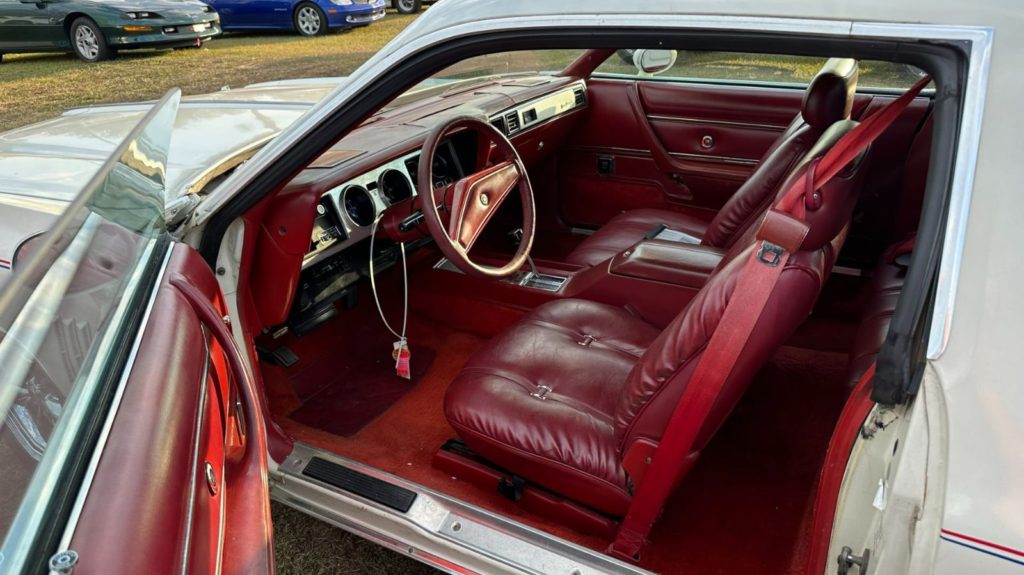
Step inside an R-body and you’d discover acres of bargain-bin plastic masquerading as luxury appointments while V8 engines consumed gasoline like a fraternity house empties kegs. These powerplants delivered horsepower numbers that would embarrass a modern lawn mower while requiring fuel stops more frequent than bathroom breaks on a road trip.
The infamous Lean Burn ignition system transformed every traffic light into a white-knuckle gambling experience where stalling wasn’t a possibility—it was an inevitability. Chrysler executives actually projected 11 defects per vehicle before these cars even left the showroom, essentially admitting they were selling guaranteed disappointment with four wheels and a warranty.
4. Ford Pinto and Mercury Bobcat (1971-1980) (Exterior)
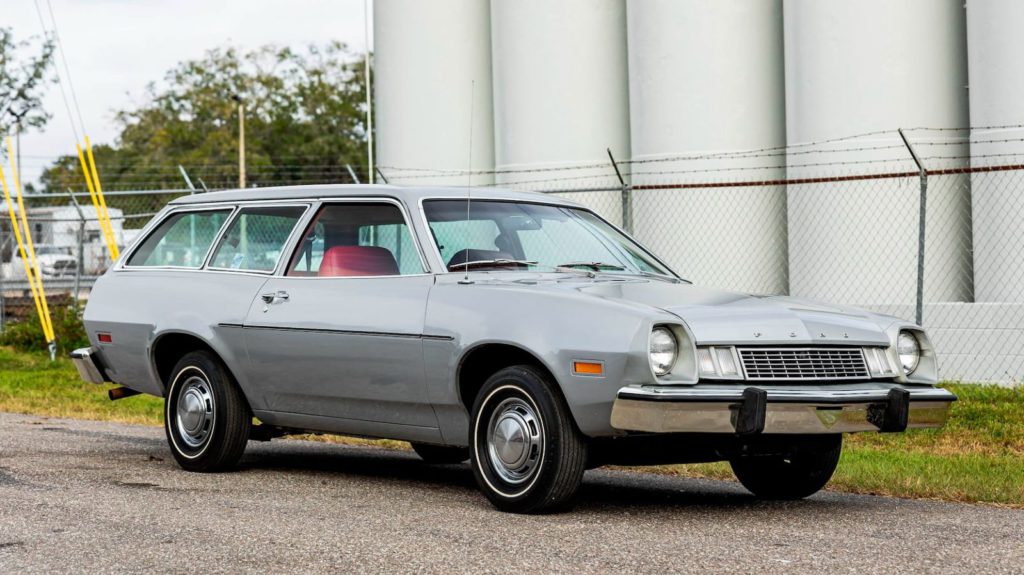
Ford’s Pinto appeared innocent enough from the outside—a compact economy car with clean lines and a distinctive fastback profile that suggested sensible American transportation for the fuel-conscious masses. The design looked competent, even attractive, for what it was supposed to accomplish in the marketplace.
What lurked beneath that seemingly harmless exterior was corporate cost-cutting disguised as practical design, with a fuel tank positioned like a ticking incendiary device behind the rear axle. This wasn’t just poor design—it was a calculated risk that turned routine fender-benders into potential crematoriums on wheels.
Ford Pinto and Mercury Bobcat (1971-1980) (Interior)

Inside, the Pinto offered spartan but functional transportation with typical 1970s build quality and performance that disappointed compared to most competitors in its class. The real horror story wasn’t happening in the cabin, though—it was unfolding in Ford’s boardrooms where executives weighed human lives against balance sheets.
Company decision-makers knew about the fire risk and calculated that an $11-per-vehicle fix wasn’t worth implementing compared to anticipated lawsuit payouts. That internal cost-benefit analysis became the gold standard for business ethics violations—a masterpiece of corporate callousness now studied in every MBA program as the definitive example of how not to value human life versus profit margins.
3. Dodge Aspen and Plymouth Volare (1976-1980) (Exterior)
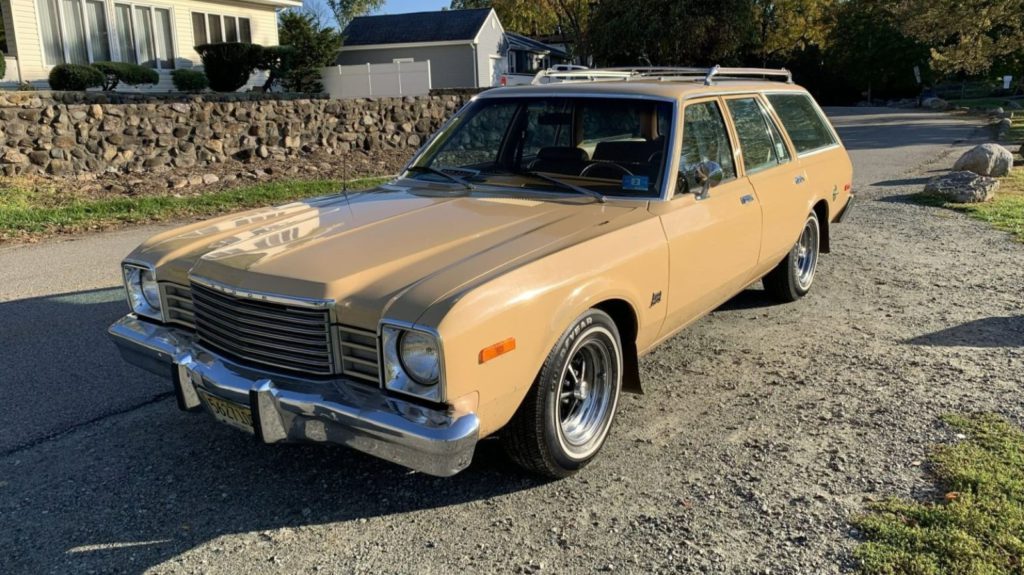
Chrysler’s compact twins promised American engineering efficiency with import-beating reliability, but delivered a masterclass in destroying brand credibility faster than you could say “rust-through warranty.” These vehicles began their oxidation process before the temporary tags expired, thanks to missing inner fender shields that saved Chrysler pennies while costing them millions in reputation damage.
Owners found themselves witnessing their Aspen or Volare disintegrate in real time, which became neighborhood entertainment in the late 1970s as bodies surrendered to corrosion with the enthusiasm of iron filings meeting magnets. The aggressive rust didn’t just affect resale values—it became automotive folklore that warned entire generations about the perils of cutting corners on fundamental engineering.
Dodge Aspen and Plymouth Volare (1976-1980) (Interior)
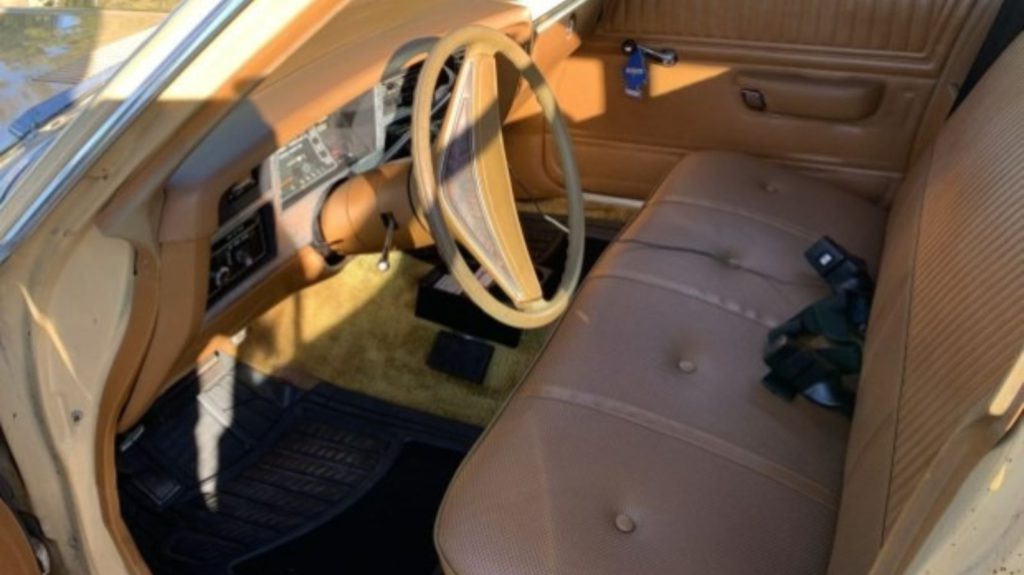
Eight recalls in their first two years tells you everything about interior reliability—these cars spent more time in service bays than driveways as owners developed Stockholm syndrome with their repair technicians. Stalling, hesitation, and throttle response issues made driving feel like operating a piece of equipment that actively resented functioning properly.
Safety recalls affected over 1.3 million vehicles for brake line corrosion, seatbelt retractor failures, and hood latch malfunctions that could turn routine maintenance into unplanned hood surfing experiences. Owning an Aspen or Volare meant maintaining backup transportation plans and developing an intimate relationship with your service advisor’s appointment calendar.
2. Chevrolet Citation (1980-1985) (Exterior)
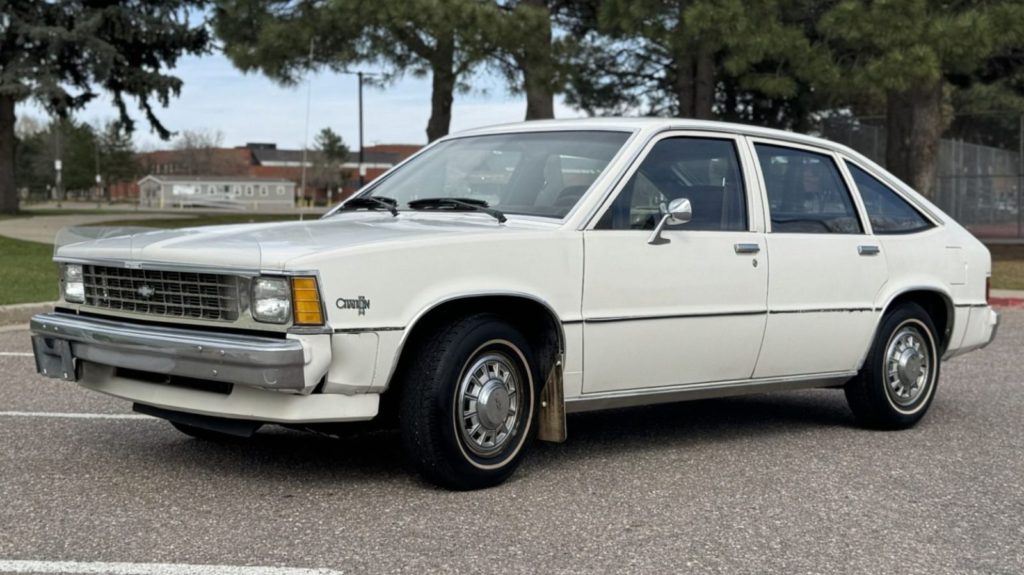
GM’s first front-wheel drive compact arrived with tremendous fanfare and initial sales of 800,000 units, sporting clean, efficient lines that suggested American automakers had finally decoded the import success formula. The Citation looked competent enough to convince buyers that Detroit had learned its lessons about modern automotive design.
Those impressive sales figures masked a ticking time bomb of quality issues that would detonate spectacularly in showrooms nationwide. Within just a few years, sales plummeted from 800,000 to 200,000 units as word spread faster than gossip in a small town about the Citation’s numerous mechanical shortcomings and reliability failures.
Chevrolet Citation (1980-1985) (Interior)

Four and six-cylinder engines delivered performance so uninspiring they made watching paint dry seem exciting, while developing a reputation for braking and steering problems that transformed routine commuting into extreme sports. The Citation earned the distinction of becoming one of the most recalled vehicles of its era, a title no manufacturer wants on their resume.
Quality concerns multiplied as these cars aged about as gracefully as milk left in summer heat, with rear brake lockup and handling issues that made every trip feel like an audition for a demolition derby. GM discovered that impressive launch numbers mean absolutely nothing if your product can’t maintain consumer confidence beyond the honeymoon period.
1. Chevrolet Vega (1971-1977) (Exterior)

If automotive disasters maintained a hall of fame, the Vega would occupy its own dedicated pavilion complete with interactive rust exhibits and engine failure simulations. Bodies developed corrosion faster than time-lapse photography of decaying fruit, often displaying significant oxidation damage within the first two years of ownership. It was a fate shared by some wild pickup truck experiments that also pushed the limits of reliability and design.
Front fenders and body panels surrendered to the elements so rapidly that “Vega rust” entered automotive vocabulary as shorthand for premature deterioration that defied both logic and warranty coverage. Observing these cars dissolve in real time became a tragic form of entertainment that damaged GM’s reputation more thoroughly than any competitor’s advertising campaign ever could.
Chevrolet Vega (1971-1977) (Interior)

The aluminum engine block lacked proper cylinder liners, creating a perfect storm of overheating and oil consumption that made routine maintenance feel like emergency room triage. Mechanical reliability failed across multiple systems with such predictable regularity that Vega owners formed their own support networks for coping with automotive trauma.
Engine problems became so commonplace that parts stores stocked Vega components like emergency medical supplies, while the car’s numerous quality failures served as a sobering reminder that innovative materials mean nothing without proper engineering execution. While automotive folklore may exaggerate some failure stories, the core reliability issues were documented thoroughly enough to fundamentally alter American consumers’ perceptions about domestic versus imported manufacturing standards.