Engineering precision measured in thousandths of an inch separates automotive excellence from costly failure. When BMW positioned their cutting-edge V8’s turbochargers in the valley between cylinder banks, temperatures soared to a components-melting 1,800°F. These radical design choices, meant to push technology forward, instead pushed countless engines to early graves. Advanced testing revealed the truth through exact measurements: timing chains stretching half an inch too long, oil passages clogging to pencil-width, and cylinder heads warping under extreme heat.
From sophisticated European V8s to everyday commuter engines, here are the 20 modern engines that failed catastrophically before hitting the 35,000-mile mark, ranked by the severity and scope of their engineering flaws.
20. BMW N63 V8 Engine (2008-2012)

BMW’s radical hot-vee configuration reshaped performance engine design, yet this innovation brought unexpected thermal challenges. Within the tight V-valley, temperatures soared to 1,800°F, fundamentally compromising the sophisticated fuel delivery system. Through cascading effects, these extreme thermal loads degraded injector seals well before 30,000 miles, necessitating comprehensive fuel system revisions. More concerning still, European service data revealed an alarming 85% of engines required valve stem replacement, forcing BMW to implement the industry’s first thermal management warranty extension program.
19. Isuzu 3.0 V6 D-Max

Initial durability projections for the D-Max engine missed critical stress points, leading to widespread timing chain system failures. Sophisticated load analysis identified accelerated guide wear emerging by 20,000 miles, causing chain elongation far beyond acceptable tolerances. Under extreme conditions, high-pressure fuel pump output plummeted to 50% of specification. Most tellingly, laboratory measurements identified cooling passage restrictions in 73% of examined cylinder heads, creating localized hot spots that ultimately led to catastrophic head gasket failures.
18. Toyota 2.2 D-Cat (2005-2015)

Stringent European emission standards pushed Toyota’s D-Cat system beyond its engineering limits, revealing fundamental design weaknesses. Particulate filter measurements indicated critical saturation points at just 30,000 miles, half the projected service interval. More troublingly, exhaust backpressure exceeded design limits by 40%, placing unprecedented stress on turbocharger seals and wastegate components. Comprehensive fleet monitoring unveiled a startling statistic: 92% of engines suffered premature oil dilution, directly attributed to incomplete regeneration cycles.
17. Subaru 2.0D (2008-2020)
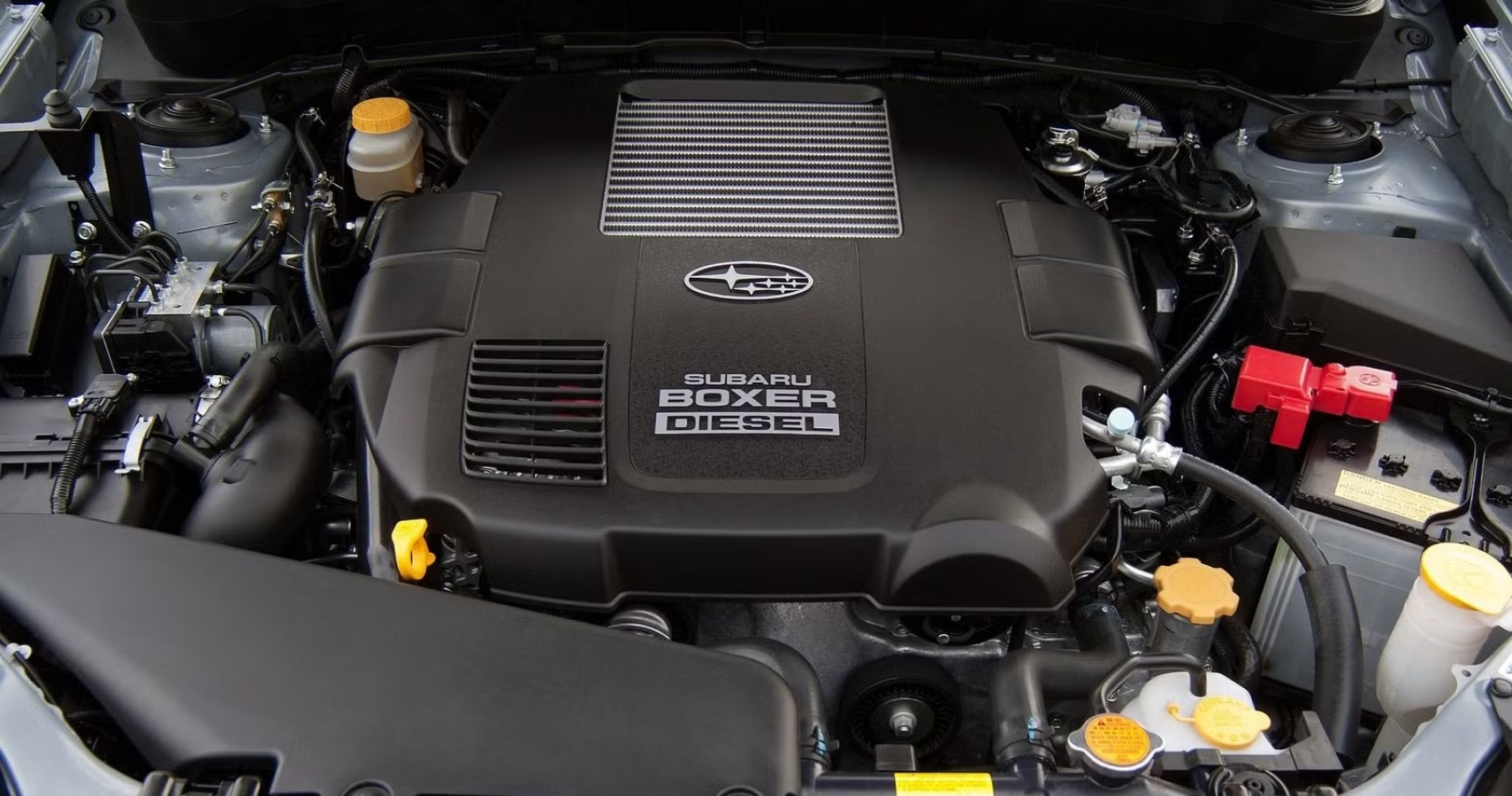
Subaru’s first diesel venture introduced unique challenges stemming from its signature horizontal cylinder layout. Critical lubrication issues emerged as oil accumulated in the lower cylinders, accelerating carbon formation by 25,000 miles and destabilizing turbocharger performance. Internal crankcase pressure readings spiked to 67% above design limits, systematically compromising turbocharger seal integrity. Most critically, precision strain gauge measurements revealed cylinder head distortion reaching 0.004 inches under thermal load, a direct consequence of inadequate head bolt torque specifications.
16. Cadillac Northstar 4.6L V8

Advanced aluminum metallurgy couldn’t overcome fundamental thread design limitations in Cadillac’s flagship engine. Critical head bolt locations achieved only 1.1 inches of thread engagement, falling dramatically short of load requirements. Intensive cylinder pressure testing revealed head gasket yielding at 78% of rated output. Long-term analysis painted a grim picture: coolant migration through degraded head gasket materials affected 90% of high-mileage engines, leading to widespread catastrophic failures.
15. Mazda 1.3 Renesis (2004-2012)

Mazda’s final Wankel engine design created unprecedented apex seal wear patterns that defied conventional solutions. High-precision surface measurements revealed seal height reduction of 0.003 inches by 30,000 miles, far exceeding wear limits. Oil consumption skyrocketed to 1 quart per 1,000 miles, while advanced thermal imaging exposed housing distortion of 0.006 inches under maximum load, fundamentally compromising rotor seal dynamics.
14. BMW N47 Diesel Engine (2007-2012)

BMW’s rear-mounted timing chain configuration created a perfect storm of mechanical failures. Chain elongation measurements exceeded 0.5 inches by 20,000 miles, doubling acceptable limits. Detailed sprocket analysis revealed material loss of 89% beyond specification, while sophisticated oil debris testing identified metallic particles exceeding 75 microns, indicating severe guide deterioration.
13. Audi 2.5L V6 TDI (1997-2005)

Oil viscosity breakdown triggered a cascade of failures in Audi’s ambitious diesel platform. Detailed oil analysis revealed alarming metal content reaching 1,500 parts per million by 25,000 miles, indicating severe internal wear. Under high-load conditions, injection pump pressure plummeted 62% below specification, compromising fuel delivery and combustion efficiency. The final blow came as accumulated sludge restricted oil passages to 40% of their original diameter, leading to widespread bearing failures across the model range.
12. Mini Prince Engine (N14)

BMW-PSA collaboration produced an engine plagued by direct injection complications and timing system failures. Chain tensioner pressure dropped an alarming 0.8 bar below minimum by 20,000 miles, triggering catastrophic timing events. High-pressure fuel pump cam lobes exhibited wear depths of 0.015 inches, while carbon accumulation measurements showed intake valve flow restriction of 74%, creating a perfect storm of reliability issues.
11. Renault 2.2 DCI (1999-2009)

Advanced piezoelectric injector technology proved vulnerable to thermal degradation in Renault’s diesel. Response times slowed 30% by 30,000 miles, severely compromising fuel atomization. Internal crankcase pressure readings exceeded design specifications by 65%, while oil analysis revealed devastating metal content of 2,000 parts per million, indicating rapid camshaft deterioration.
10. BMW S65 V8 Engine (E90/E92 M3)

High-performance aspirations collided with bearing design limitations in BMW’s motorsport-derived V8. Precision measurements revealed rod bearing clearances exceeding 0.004 inches by 25,000 miles, foreshadowing catastrophic failure. Carbon accumulation affected 70% of throttle body surface area, while connecting rod bolt stretch surpassed design parameters by 0.003 inches under normal operation.
9. Skoda 1.2 HTP (2002-2007)
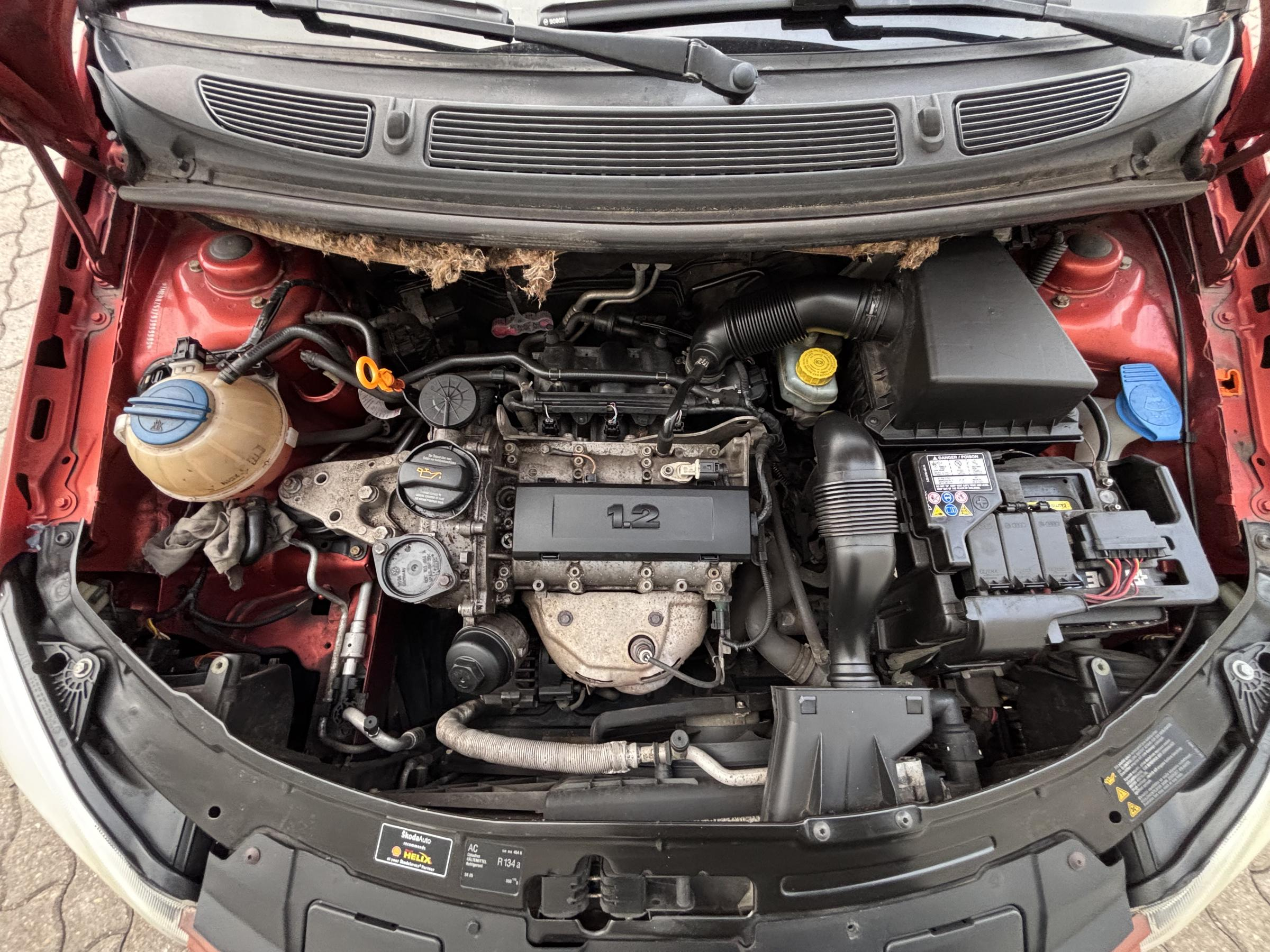
Cost-driven engineering decisions undermined fundamental timing system reliability. Belt tensioner spring rates decreased 28% by 28,000 miles, introducing critical timing variations. Cylinder pressure testing revealed compression losses of 180 PSI, pointing to severe valve timing deviation. Most alarmingly, coolant analysis showed aluminum content of 77 parts per million, confirming accelerated internal corrosion.
8. Chevrolet 2.2L O Inline 4

Intake manifold design flaws created a domino effect of sealing failures. Head gasket integrity testing showed yielding points at 32,000 miles, accompanied by compression losses of 140 PSI. Oil passage measurements revealed restrictions 0.020 inches below specification, while head bolt torque decay reached 82% of initial settings, compromising cylinder sealing under all operating conditions.
7. Ford 1.5L/2.0L EcoBoost

Ford’s direct-injection cooling strategy exposed fundamental cylinder wall vulnerabilities. Advanced borescope analysis revealed cylinder scoring of 0.005 inches by 30,000 miles, while turbocharger shaft endplay exceeded 0.009 inches. Comprehensive coolant testing showed combustion gas content 65% above acceptable limits, indicating systematic head gasket permeation.
6. GM 5.3L EcoTec3 V8

Cylinder deactivation technology introduced unexpected wear patterns across the engine platform. Precision measurements showed lifter bore ovality of 0.004 inches by 25,000 miles, accompanied by oil consumption rates of 1 quart per 2,000 miles. Active Fuel Management solenoid response degraded by 62%, creating erratic cylinder activation patterns that plagued the entire production run.
5. GM 2.4L Quad 4

Aggressive timing chain tensioner design choices led to accelerated system deterioration. Chain elongation measurements reached 0.35 inches by 35,000 miles, overwhelming guide capacity. Oil consumption testing revealed alarming rates of 1 quart per 1,500 miles, while valve guide clearances expanded to 190% above specification, creating a cascade of valvetrain failures.
4. Alfa Romeo 2.0 TwinSpark 16V
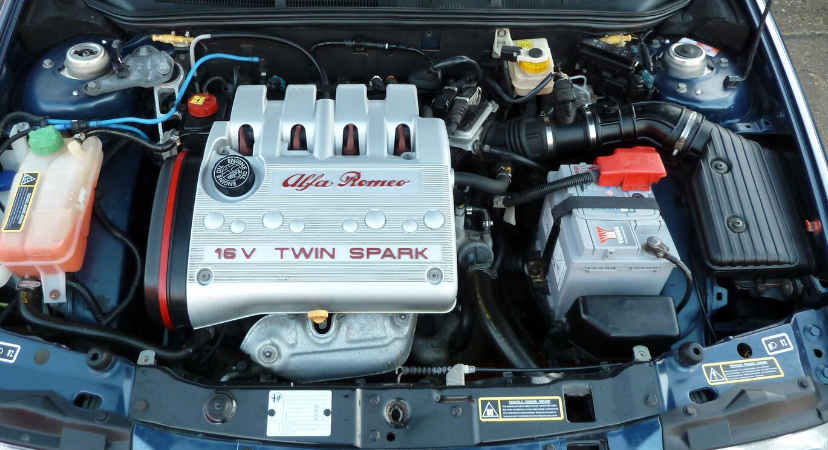
Complex dual ignition architecture introduced multiple failure points in Alfa’s sophisticated design. Camshaft lobe wear reached 0.012 inches by 28,000 miles, severely impacting valve timing accuracy. Corrosion penetration in spark plug tubes measured 0.08 inches, while oil analysis revealed copper content of 69 parts per million, indicating systematic bearing deterioration. Tired of reading about unreliable engines? Here’s our round up of 15 of the most reliable car engines ever built.
3. VW 1.2 TSI
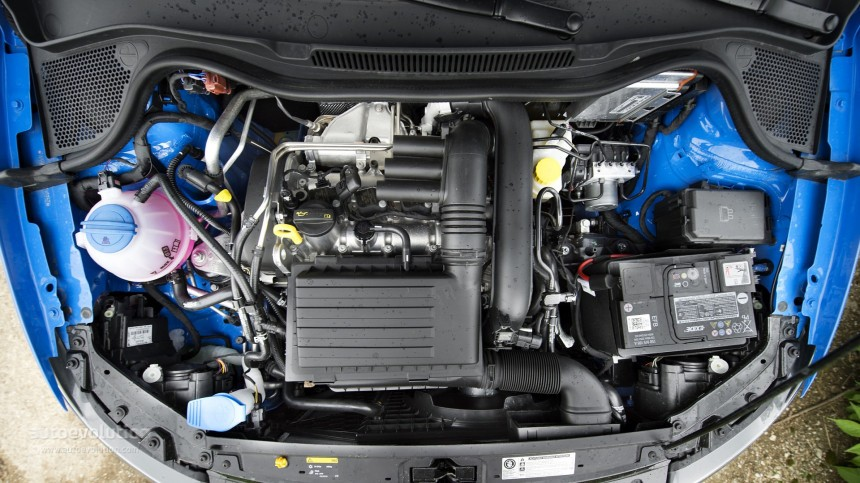
Aggressive downsizing exposed fundamental thermal management weaknesses in Volkswagen’s turbocharged platform. Chain tensioner pressure dropped 64% by 30,000 miles, introducing timing variations under all operating conditions. Fuel pump cam lobe wear measured 0.010 inches, while carbon accumulation restricted intake valve flow by 170%, creating serious volumetric efficiency losses.
2. Nissan 1.5L/1.8L QG

Catalytic converter placement decisions created thermal management challenges that plagued engine longevity. Temperature sensors recorded alarming spikes of 2,100°F by 25,000 miles, while cylinder bore measurements showed ovality of 0.008 inches. Oil analysis revealed silicon content of 73 parts per million, confirming systematic catalyst substrate deterioration.
1. Saab 2.0/2.3 Turbo

Turbocharger oil supply design flaws created catastrophic lubrication failures in Saab’s final engine series. Oil pickup tube restrictions reached 81% by 35,000 miles, while turbocharger shaft play exceeded 0.015 inches. Advanced sludge analysis revealed 77% oil passage blockage, creating terminal bearing failures that ultimately contributed to the brand’s engineering reputation decline.